PEMTec: High Precision Electro Chemical Machining Solutions
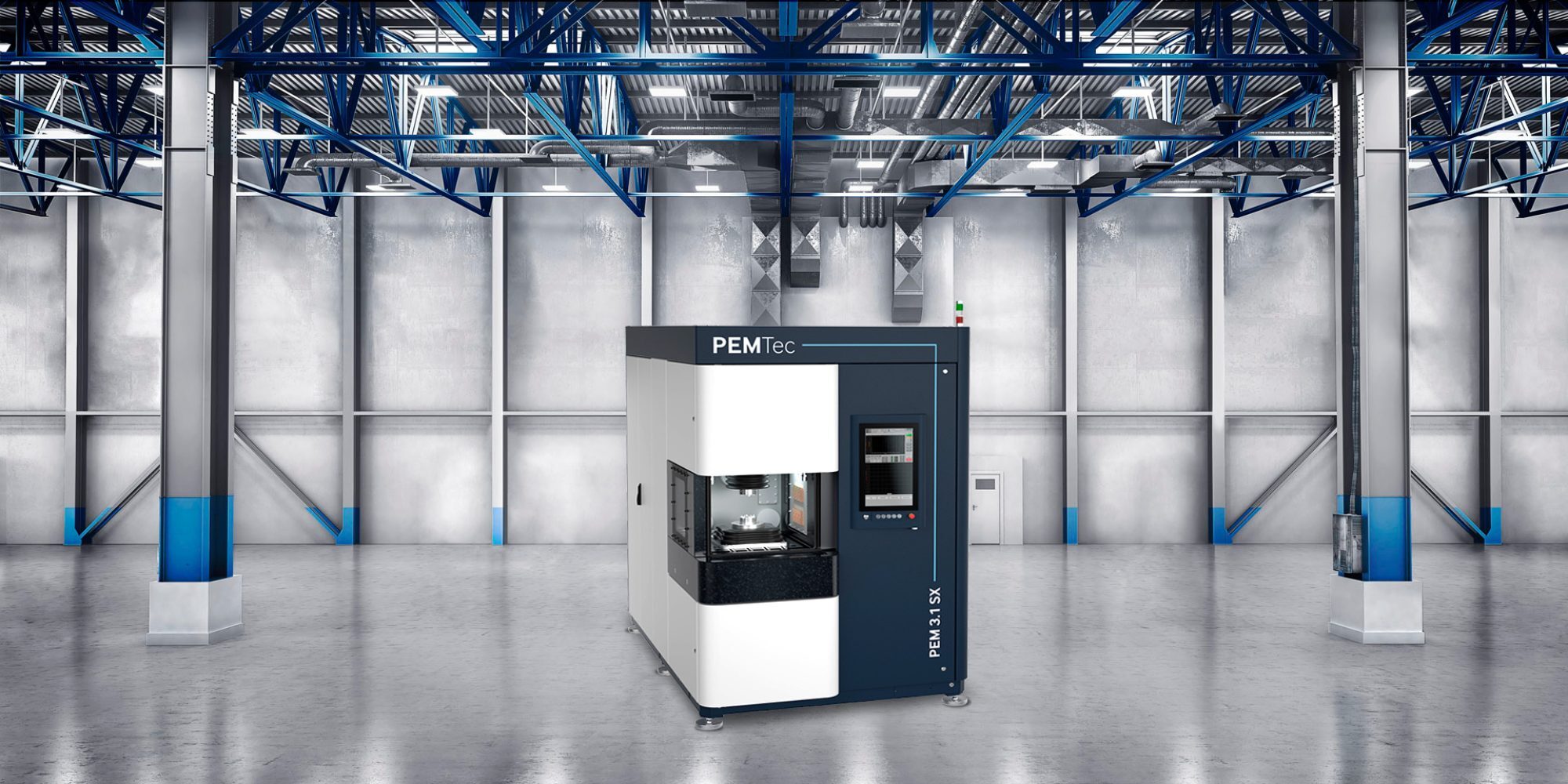
Company Overview
and History
Across industries like aerospace, automotive and medical, the demand for ultra-precise machined parts continues to grow. While traditional CNC machining offers impressive accuracy, the PECM (Precision Electromechanical Machining) process takes accuracy and efficiency to a new level, shaping metal workpieces with micro-level accuracy, all without any physical contact between the tool and the material.
Pioneered by leading German manufacturer PEMTec, this technology, often referred to as “pemming” to differentiate it from more traditional contact methods, uses a saltwater electrolyte and an electrical current to dissolve material from the workpiece, which takes on the inverse shape.
This non-contact application for metal removal and the superior level of accuracy it confers is becoming increasingly popular with high-precision manufacturers who work with hard-to-machine materials, parts with complex geometries and those where precision is paramount, such as medical components, turbine blades or fuel injection nozzles.
Overview of PEMTec Machines
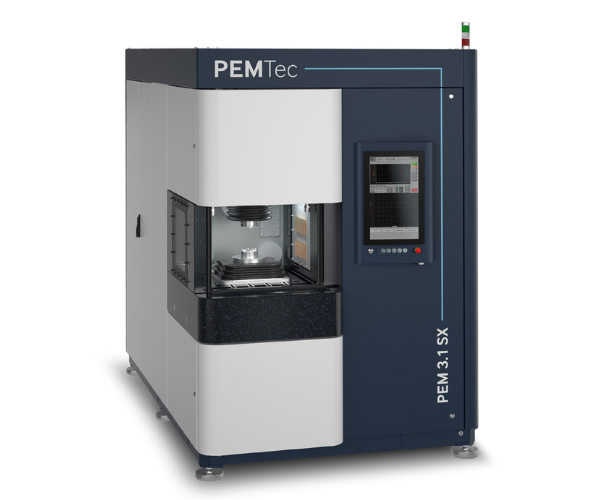
PEM 3.1SX
The 3.1 SX offers PECM technology and its inherent accuracy in a compact footprint of under 3m.
Key Advantages:
- Compact all-in-one machining solution with a small footprint
- Machining of a very wide range of metals regardless of their hardness
- High-precision mapping of the finest geometries and structuresRoughing, finishing and polishing sequentially (in one operation)
- No melting, no micro-cracks, no formation of external phase
PEM 3.1 SX CC
This machine has been developed exclusively for the precise machining of cemented carbide, delivering high-precision machining results without cracks or microscopic structural damage.
Key Advantages:
- All the benefits of PEM 3.1 SX
- Dust-free formation during machining
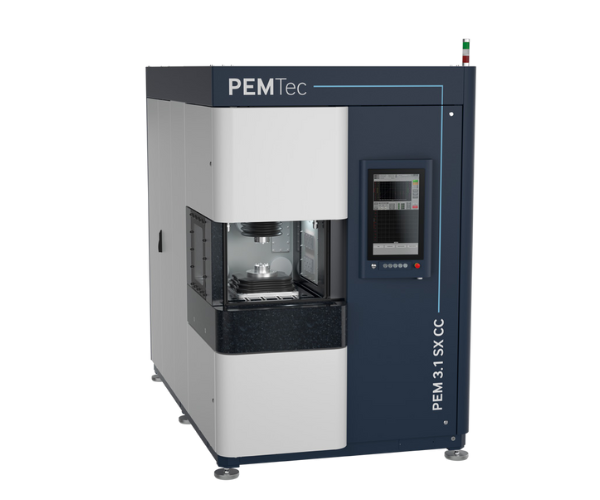
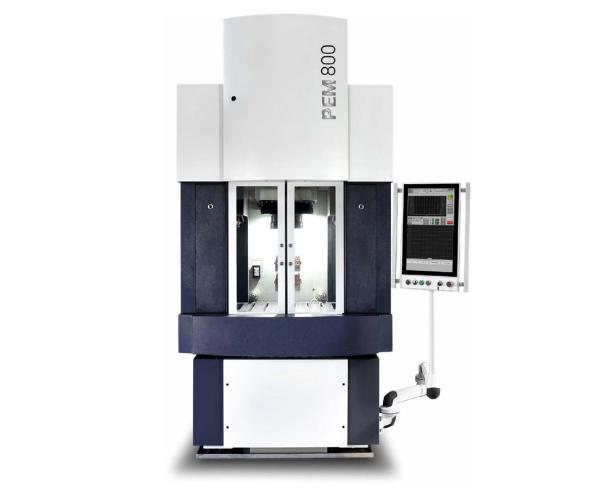
PEM 800
The PEM 800 is considered the big brother of the range with a larger working area to allow the use of bigger tools and a 9600A generator.
Technical Data:
- Machine frame constructed from natural granite
- Working space 375 – 545 mm (min/max)
- Machining table 660 × 540 mm (W×D)
- Required space 2,200 × 2,560 × 2,870 mm (W×D×H),
excluding electrolyte preparation (see description PEMAQUA) - Maintenance-free precision work axis with direct drive
Download the entire technical datasheet below.
PEM 800S
The PEM 800 S is the newest and most technologically advanced of PEMTec’s machines. It has a higher axis force and improved pulse rate to remove more material during the process.
Technical Data:
- Every feature PEM 800 has.
- Highly rigid, high-precision working axis with central direct drive.
- Temperature compensation for the machine frame and process axis
Download the entire technical datasheet below.
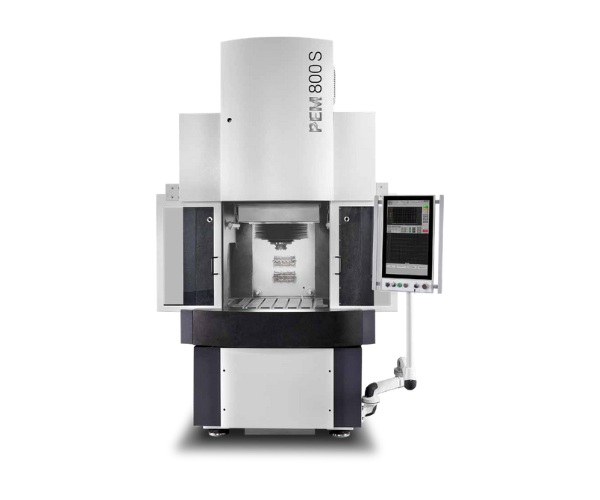
.png?width=604&height=604&name=Untitled%20design%20(24).png)
PEM AQUA
The components, machine and electrolyte
treatment are developed, thoroughly tested and
manufactured by us. Our systems are guarantors
for quality. Equipping that machine with exactly
the number of microfilters required and the fully
automatic monitoring and precise adjustments of
the elektrolyte‘s conductivity, pH-value, chromate,
content and temperature are matter of course of us.
The machine and electrolyte treatment need to be
optimally attuned.
Advantages of PECM Process
While PECM machining achieves the same result as contact CNC machining – a highly accurate finished part – it has several distinct advantages:
-
Precise machining of almost all metals – PECM can work with most metals regardless of hardness, including superalloys (Inconel, Hastelloy, etc) and PM steels
Micron-level accuracy – The technology enjoys a standard created surface quality up to Ra 0.03 µm and offers highly accurate reproduction and high-quality surface finish every time
Burr-free – No chips or burrs, reducing the need for secondary processing
No thermal damage – As the process is non-thermal, there is no risk to heat-affected zones
Stable workpieces – With no mechanical or thermal strain, there are no microscopic changes to the structure of the workpiece, which could affect lifespan or integrity
Time saving – Short processing times with a single workflow (roughing, finishing and polishing). Also capable of simultaneously manufacturing macro/microstructures
Versatile – Suitable for prototyping, short production runs and serial manufacturing
Extended tool life – There’s no wear and tear on tools or chemicals used in the process
About PEMTec’s And Rainford’s Partnership
Brochure Downloads
Looking for more technical details? Download our free PEMTec brochures for in-depth specifications, features, and application insights
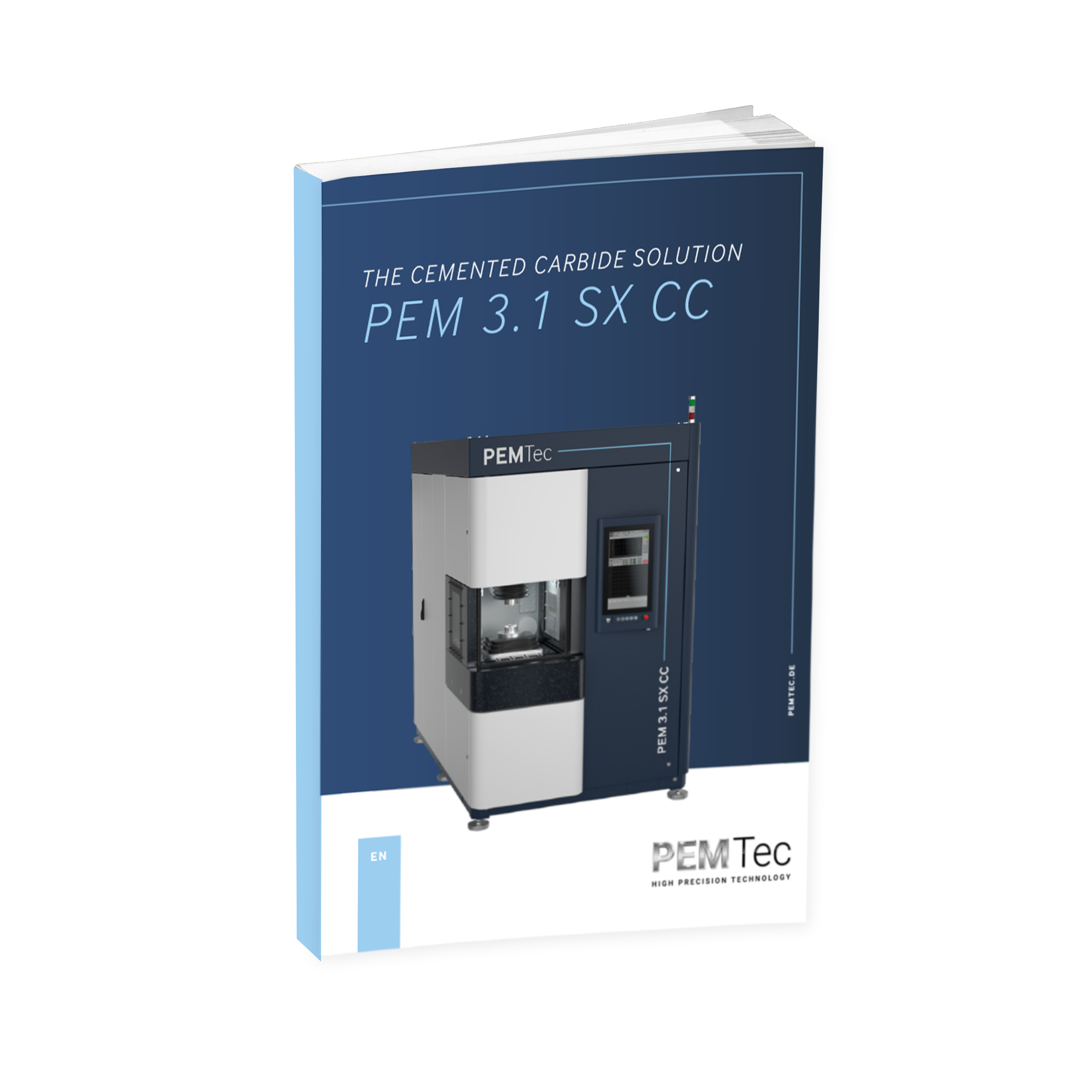
PEM 3.1 SX CC
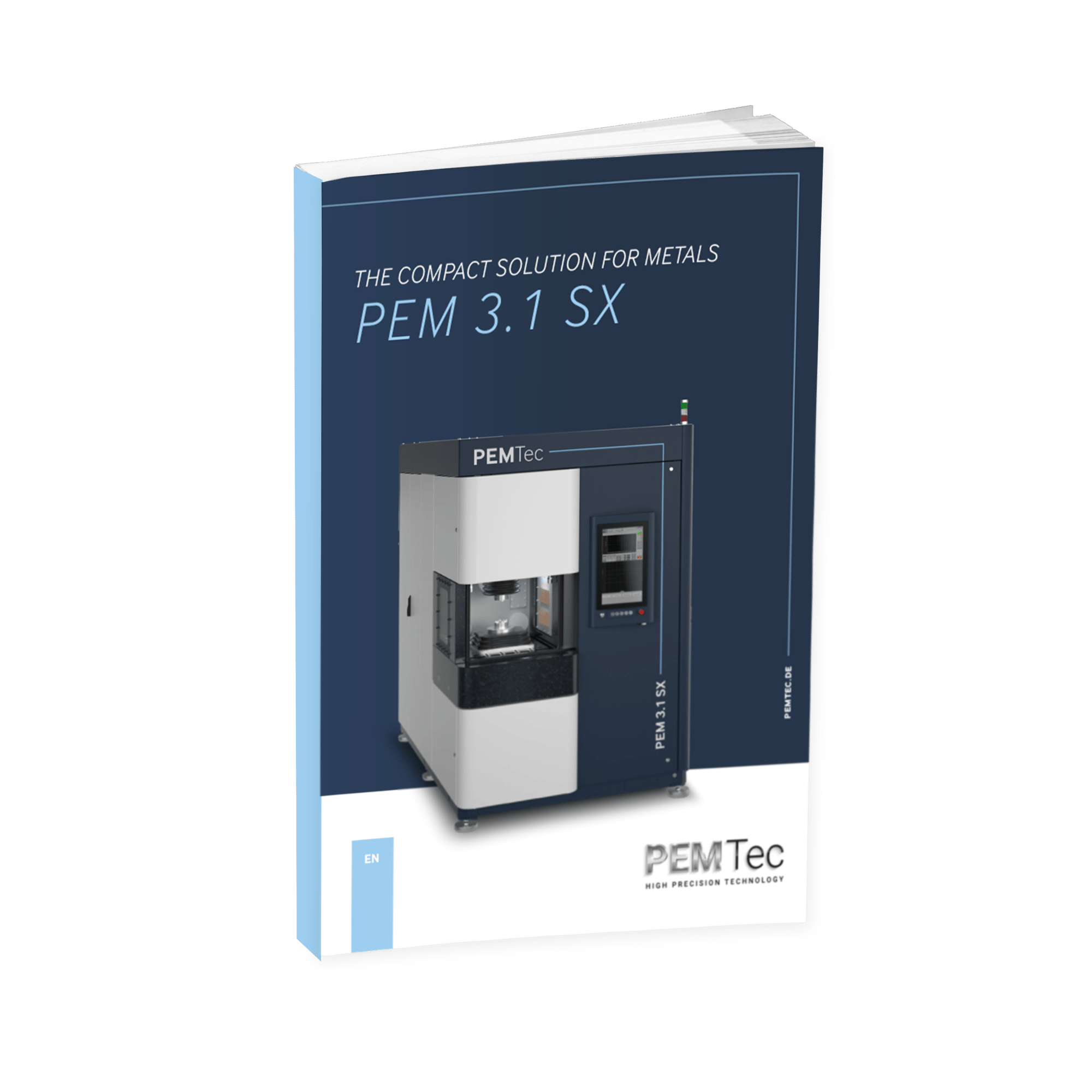
PEM 3.1 SX
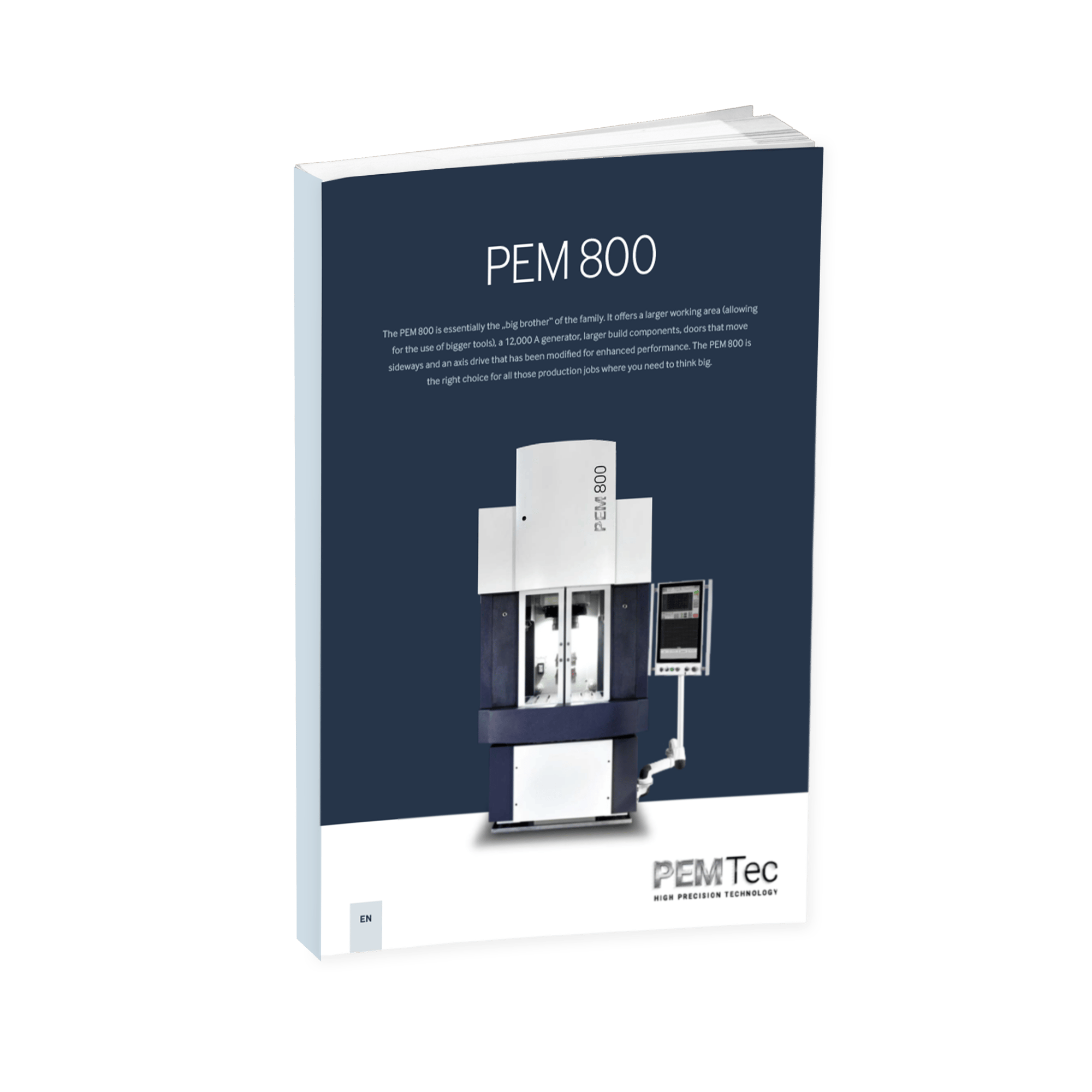
PEM 800
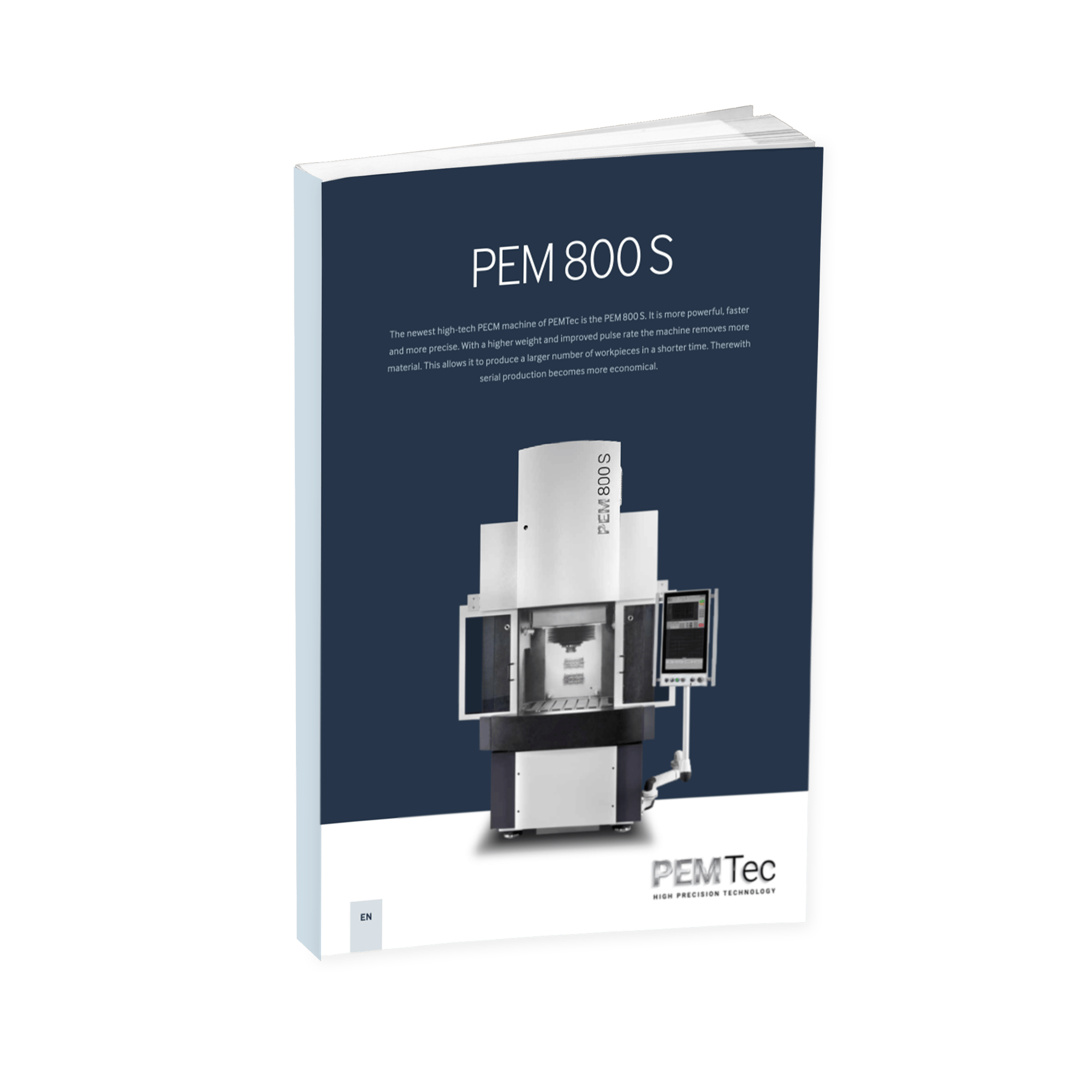
PEM 800s
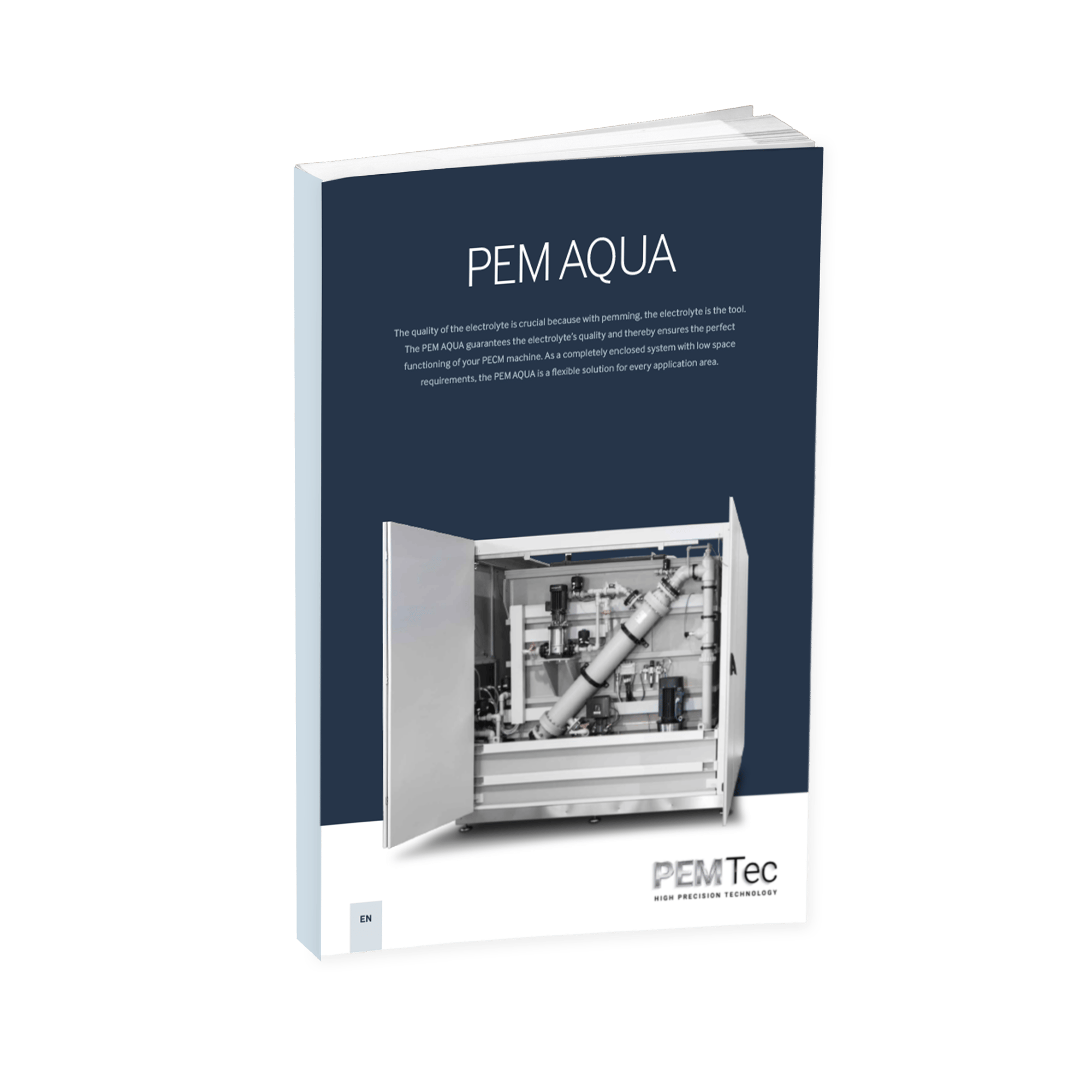
PEM AQUA
Why We Do What We Do
I would like to say thank you for your assistance so far. We have only drilled 4 x 0.80mm holes 50d deep but the fact they worked the first time was appreciated by everyone.
We use OSG mainly but when we have a specific job that needs doing, we come to Rainford Precision because they are and do the Crème De La Crème of Products and services.
The End Mill was an ideal choice due to the unusual shape and the need to have a small radius. They turned out great, and the surface finish is really good.
I would like to say thank you for the help you have given our project over the last few years. Your advice on the correct cutters plus the right speeds and feeds has not only helped with accuracy but brought the cycle times down so we can meet our project deadlines.
Thank you for making that so incredibly easy and prompt.
We received your delivery this morning as you had promised to do for us, thanks for that, it is great when a plan comes together.
A diamond service from Rainford as usual. The success of our company is very much down to the external support received from Key organisations such as Rainford Precision. Your company is one of the first I will always turn to assist us.
Book A Consultation
Revolutionise your machine drilling operations today! Take the first step by booking a consultation and a member of our seasoned team will analyse and optimise your processes, recommending cutting-edge technologies for enhanced precision and productivity.
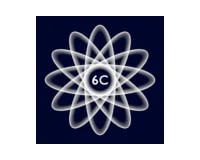
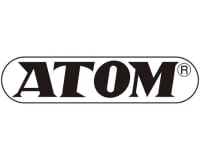
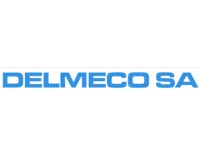
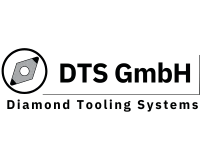
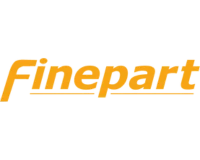
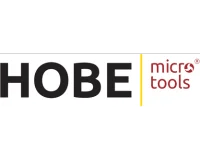
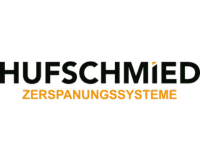
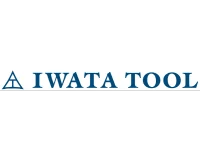
.png?width=2563&height=2351&name=KERN-Ametek-logo-rot-schwarz%20(1).png)
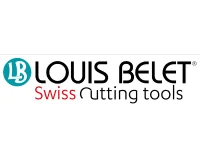
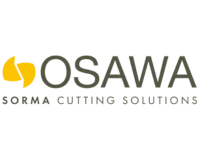
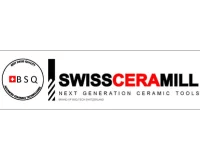
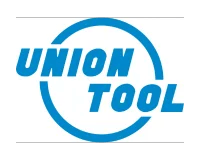
.png?width=500&height=200&name=PEMtec%20Logo%20(1).png)
.png?width=500&height=200&name=Benzinger%20Logo%20(1).png)
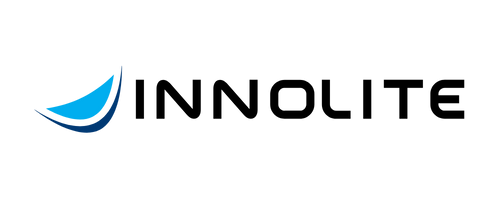
Interested In Our Products?
Get access to our wide range of product brochures
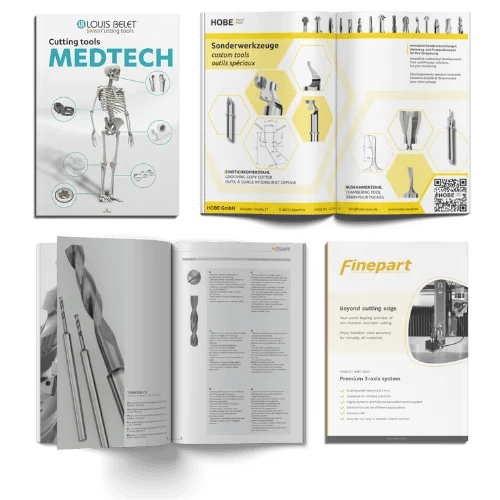
Latest From The Blog
2 min read
Fuelling Innovation In Medical Equipment Manufacturing With High Precision Cutting Tools
Apr 25, 2025 by Rainford Precision
2 min read
Louis Belet: Precision Tools For Every Stage Of Watchmaking
Apr 21, 2025 by Rainford Precision